Dry Shotcrete
TARGET® SUPERSTICK® Shotcrete (9991320) produces a range of bagged dry shotcrete mixes for use in either dry-mix or wet-mix shotcrete processes. Shotcrete aggregates are blended to ACI 506R 90 gradation requirements and shotcretes are available in either ACI Gradation No.2 (medium) or Gradation No.1 (fine) aggregate gradations.
- Dry Shotcrete Equipment
- Dry Shotcrete Machine
- Dry Shotcrete Vs Wet Shotcrete
- Dry Shotcrete Mix Design
- Shotcrete Dry Process
Ask The Expert
#shotecrete #gunite #concrete #plaster #concretefinishing #navneetvideos #structures #SteelfibreReinforcedShotcrete #SFRS #ReinforcedShotecrete #CivilEnginee. Shotcrete has often been described not as a material but as a process. Both wet and dry processes produce a material that exhibits superior hardened properties to high quality conventional concrete, such as high strength, low permeability and high durability.
Wet Process VS Dry Process Shotcrete
Shotcrete was invented in the early 1900’s by American taxidermist Carl E. Akeley by propelling a dry material through a hose with water injected at the nozzle to fill plaster models of animals. Soon after, it was discovered the same method was an effective way to repair buildings. In 1911, Akeley was granted a patent for his invention, originally called the “cement gun,” and the shotcrete industry was born.
Shotcrete is an excellent repair method when compared to traditional cast in place methods. It provides high bond strength, increased compressive and flexural strength and increased resistance to chemical and alkali attack. It requires little or no formwork, which makes shotcrete traditionally faster than cast in place. Shotcrete also offers a myriad of sustainability benefits. Wet process or dry process shotcrete can both provide a viable, cost effective, and durable solution for many design requirements.
The American Concrete Institute (ACI) defines shotcrete as “mortar or concrete pneumatically projected at high velocity onto a surface.” Shotcrete is used in multiple arenas of construction including, but not limited to repair and restoration, mining underground and tunneling, new construction, and refractory. The two types of shotcrete processes, dry shotcrete (also known as gunite), and wet shotcrete, have grown steadily in popularity in both concrete repair and new construction. This article will compare and contrast the two shotcrete processes.
Dry process is defined by the ACI as “shotcrete in which most of the mixing water is added at the nozzle.” Dry ingredients are placed in a hopper and then are pneumatically propelled through a hose to the nozzle. The nozzleman then controls the addition of water manually at the nozzle. Wet process is defined by the ACI as “shotcrete in which all of the ingredients, including water, are mixed before introduction into the delivery hose and compressed air is introduced to the material flow at the nozzle.” In other words, dry process involves blowing powder through a hose and adding water at the nozzle, wet involves pumping already mixed material to the nozzle. Compressed air is introduced at the nozzle during wet process to enhance the spray characteristics. The main difference between the two processes is the point at which the water is added.
When selecting a method of placement, finished product is rarely the exclusive consideration. Other than a few small technical differences, the material is all generally the same once it hits the substrate regardless of application method. The determining factors are scope of work, availability of materials, availability of equipment, site access and contractor preferences.
Often one of the most important considerations in shotcrete selection is the scope of work. Each application is unique and quantity is often a factor. Advances in concrete pumps have allowed for faster placement of wet process material. This higher production rate tends to make wet process the preference on larger jobs. Many lock and dam, underground and rail tunnel projects require hundreds or even thousands of yards of material placed in large wide open areas. In many of these applications, aesthetics are not a primary concern, so the shotcrete is not given any type of trowel finish and is left with a natural gun finish. The speed of placement with wet process is attractive to contractors on these types of projects.
Projects such as bridge pier repairs and parking garage rehabilitation often involve small areas that are finished with a steel trowel, rubber float or flash. This requires the contractor to stop the shooting portion of the operation in order to cut and finish the repair. Wet process shotcrete is not conducive to stop and start repairs, as each time the shooting process is stopped the hose must be cleaned of the mixed material. In addition, the entire truck must be used at once of ready mix is being used. Conversely, with dry process shotcrete the machine can be tuned off with minimal material waste as the water has yet to be added, so it is a more popular method for smaller repairs, as well as stop and start work than wet process shotcrete.
Mixes for both processes, which generally should be microsilica enhanced, are compatible with alkali resistant, polypropelene, macrosynthetic and steel fibers, and can be used with a variety of admixtures such as accelerators, integral corrosion inhibitors and retarders. Therefore, modifying a shotcrete mix to specific job requirements is not commonly a determining factor in selection, as both options offer great flexibility.
Dry Shotcrete Equipment
Material availability is another consideration. The rising cost of trucking has made it important for contractors to source materials as close to the jobsite as possible. Limited numbers of material producers in certain geographies may sway a contractor to pick a shotcrete method. Also, many projects have green initiatives in place which require contractors to source materials locally whenever possible. In some instances, local available aggregates may be insufficient to meet project specifications, which forces contractors to purchase materials from suppliers located larger distances from their location. Advances in mixers have made preblended bulk bags of material more popular on remote sites and nightshift work for wet process applications where ready mix is not available or practical.
A contractor’s personal preference is also important in selecting wet or dry process shotcrete for a project. A contractor who has more experience with one method over the other tends to prefer that method. Wet and dry process shotcrete require completely different equipment to install, so the type of equipment owned by a contractor plays a major role in the decision making process as well.
Temperatures will effect curing times of the materials making it another element in deciding on which shotcrete process is most appropriate for a job. In cold weather, shotcrete does not hang as well, especially in overhead applications, and rebound, or material that does not adhere to the substrate at which it is propelled, increases. In warmer weather, the material may require more extensive curing to prevent cracking.
Certain types of overhead locations at particular depths may lend themselves to one process or the other. Some areas are situated in a way that prevents proper nozzeling posture and distance. Sometimes in mining applications tight conditions require nozzlemen to shoot from their knees, stomachs and backs at distances either farther away or closer to the substrate than is standard. All of these unique situations play a role in selecting a process.
There is an old industry saying that “shotcrete is not a product, it is a process.” This is important to remember when specifying shotcrete work. Often it is best to let projects open to both processes at bid time. In an open competitive bid situation the best method for the application will result in the successful bid. Also, this allows a contractor to use the method they are most comfortable with, and insures the owner and architect the best opportunity to have a successful project. Some jobs clearly lend themselves toward wet process while others are more suited to dry process. Many jobs do not lend themselves to either method specifically. In other instances, wet and dry shotcrete simultaneously on a project, or are used for different phases on the same project.
As previously articulated in the article, wet shotcrete or dry shotcrete are the same when it hits the substrate. When specifying shotcrete it is important that regardless of the method you verify that the material supplier can meet the performance requirements. For starters, an ACI certified nozzlemen should be a requirement. In addition, an experience level commensurate to the project on the part of the contractor should be a requirement. On site material testing must be a part of the project and inspectors should have a basic working knowledge of the shotcrete process. For more information and advice on shotcrete specifications, please visit the American Shotcrete Association at www.shotcrete.org.
The Aliva AL-252.1 has a long tradition as the workhorse of the heavy construction industry. With an output ranging from 3.5 to 11 m³/hour (4.6 to 14.4 yd³/hour), the Aliva AL-252.1 is ideally suited for high volume, dry-process shotcrete operations. This machine is commonly used as a stand alone unit, or can be integrated into bulk-type shotcrete systems when installed on mobile equipment and fed by a bulk hopper.
• Two-axle, concrete spraying machine for dry-mix processing
• BASIC: Electric drive, combined with BASIC-Dosing unit (not synchronized)
• AIR: With air drive, combined with BASIC-Dosing unit (not synchronized)
1. HISTORY
The Aliva-252 is a sturdily constructed two-axle concrete spraying machine for the processing of dry mix.
2. APPLICATION
The machine can be used thanks to its compact design and mobility where space is at a premium e.g. in mines and galleries. Other potential applications are slope and hillside protection, lining of water tanks and swimming pools, guniting for single and double shell tunnel construction, backfilling of tubbings.
The Aliva-252 is available in the following versions:
- BASIC
Electric drive, combined with BASIC-Dosing unit (not synchronized)
- AIR
With air drive, combined with BASIC-Dosing unit (not synchronized)
3. SAFETY
Important safety regulations
For detailed informations please consult the latest edition of the machine operating manual.
4. OUTPUT
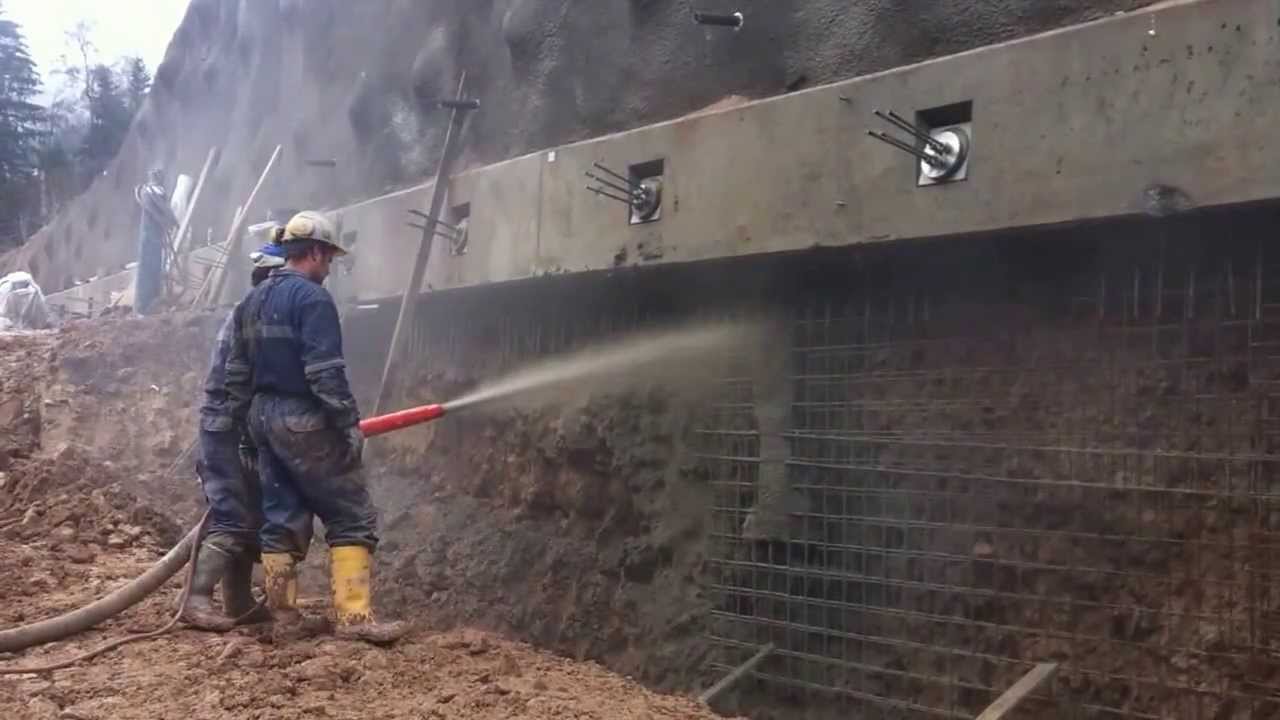
5. TECHNICAL DATA
Dimensions
With Chassis
Length L | |
with rotor 10 L | 1770 mm |
with rotor 16L | 1720 mm |
Width | 800 mm |
Height H | |
with rotor 10 L | 1310 mm |
with rotor 16 L | 1410 mm |
Weight | approx. 760 kg |
Content of hopper | 85 liters |
With Skid
Length L | |
with rotor 10 L | 1640 mm |
with rotor 16L | 1590 mm |
Width | 800 mm |
Height H | |
with rotor 10 L | 1260 mm |
with rotor 16 L | 1360 mm |
Weight | approx. 800 kg |
Content of hopper | 85 liters |
Drive
Electric (BASIC)
Motor output | 4.4 kW |
Speed range | 1500 rpm |
Voltages | 400 V 50 Hz |
400/440V 60 Hz | |
220 V 50 Hz | |
220 V 60 Hz | |
Protection | IP 55 |
With Air Motor (AIR)
Motor output | 7,5 kW |
Speed range | 900-2000 rpm |
Pressure | 4,5 bar |
Air consumption | 9 Nm³/min. |
Theoretical Conveying
_-_copy_1507998217_307547-10.jpg)
Conveying (only dry)
Rotor L | Hose Ø Mm | Conveying Output *m3/h | Max. grain Mm | Max. conveying distance (m) Horizontal/vertical | ||
BASIC | AIR | |||||
10 | 50 | 5 | 3.5 – 7.0 | 16 | 300/100 m** |
Dry Shotcrete Machine
*with theoretical filling degree of 100%, if motor with 60 Hz = 20% higher conveying capacity.
**more than 80 m conveying distance, use steel tubes.

Theoretical Air Consumption
Hose Ø Mm | Air Consumption Nm3/min.*** | |
Dry Spraying | ||
60 m | 120 m | |
50 | 8 | 10 |
60 | 11 | 13.5 |
*** Air consumption data are approximate values and are depending on conveying output, conveying distance and hose diameter.
Caution: For the configuration AIR (with air motor) it has to be considered:
Total air consumption = Air consumption for conveying + Air consumption for air motor! 1 Nm3/min = 35 cfm
Contact Us
For technical support services pertaining to any machine or piece of equipment offered, e-mail kingshotcrete@kpmindustries.com

Dry Shotcrete Vs Wet Shotcrete
Related Products
Dry Shotcrete Mix Design
